Cigars, Cuba

Dividing tobacco leaves, Partagas Cigar Factory, Havana, Cuba — May 21, 2003
These tobacco leaves are sorted into four piles: taste, burn, fiber and color.
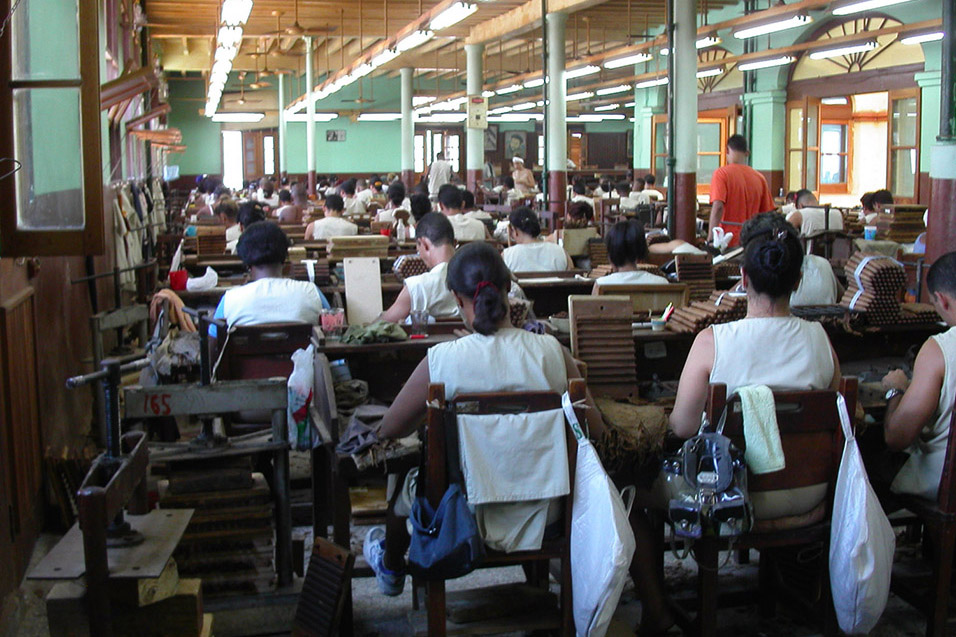
Main rolling room, Partagas Cigar Factory, Havana, Cuba — May 21, 2003
Photos were forbidden, so I had to sneak this one.
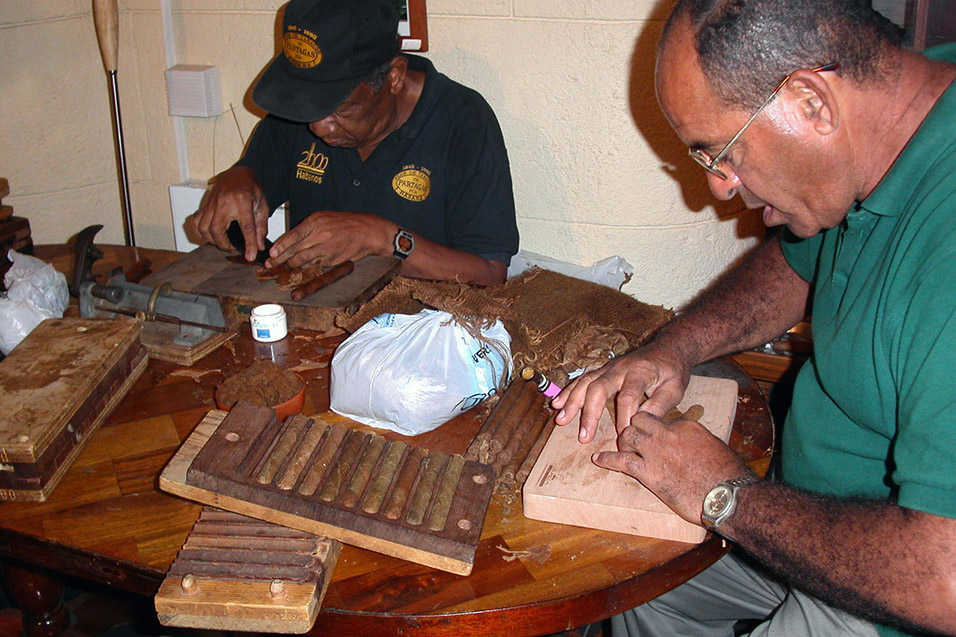
Rolling and pressing cigars, Partagas Cigar Factory, Havana, Cuba — May 21, 2003
Every cigar made in Cuba is hand-rolled; that is what makes them so special (and so expensive.) The government owns every brand of cigar, so the Partagas Cigar Factory produces the Cohiba, Montecristo and Romeo & Juliet brands right next to each other. Only an expert can tell them apart before they are labeled, but this factory is filled with experts. The tour highlights every step of the cigar making business:
- The bottom floor is receiving. Waxed boxes of tobacco arrive from all over Cuba, especially the Pinar del Rio region.
- Tobacco leaves are then divided by characteristic. The five main piles include leaves used for: color, taste, burn rate, fiber/filler, outer rolling leaves.
- The second floor holds the main rolling room. Hundreds of workers (all paid $8/month) meticulously roll the various cigar brands. Each cigar is comprised of four leaves: color, taste, burn rate, fiber. These four leaves are bundled together in a cylindrical shape and placed in a press for at least ½ hour. Brands have varying press times.
- Pressed cigars are removed and the outer leaf is applied in a diagonal fashion so that one leaf covers an entire cigar.
- The tip has an addition tobacco bit wrapped around it. Non-toxic tree sap is used as an adhesive glue. Workers are expected to produce between 180 and 240 cigars a day. Each worker identifies daily quotas by applying a temporary label around their bundle of cigars.
- Adjacent the rolling room is quality control (QC). Cigars are first checked by humans for color, size, shape, etc. Randomly selected cigars are placed in a machine that tests for draw by applying suction. Cigars that fail are returned to the worker for further scrutiny.
- A small room behind has a seat where one elderly man sits with a cigar in his mouth. He wears a big smile as he waves to all the tourist. It is explained that this man is the official taster. He is an absolute expert and it is his job to randomly smoke the cigars the factory produces. He is the final step in a comprehensive quality control.
- Cigars that pass QC are sent downstairs to packing. Piles of unused cigar boxes are strewn everywhere. Cigars receive their final branding: Labels are added. Strips of thin cedar are rolled around some cigars. Others are placed in aluminum containers, while others are placed side by side, 40 to a box.
- Upon finishing the tour, tourist are led to shop where prices range between $1 - $25 dollars for some of Cuba’s finest.
The Partagas Cigar Factory tour was one highlight of my trip and should not be missed.